In that case, I will do a detailed post on how mine is set up this weekend.
I derped quite a bit. I'm still producing almost 60 buckets of steam every clock cycle, but it is 60 combined, not per oven. I goofed on the clock itself. The clock period is on for the length of time set, then off for an equal amount of time. I was thinking that it was cutting the time in half for some reason.
Oh well. I was still producing a bunch of steam, and still powering my whole base off of it, so it worked.
I am using an MFR rednet controller to run everything. Before, my thinking was to have the rednet turn the water source on and off, then throw massive amounts of fluiducts to drain all the water out of the ductwork. Instead, I realized that you can keep the duct work full of water at all times, but just enable and disable the filter. To do this, you need to add servos to all the drains that will be supplying water. Normally when adding servos and filtering fluiducts, you place the redstone control in the ignored mode. In this case however, you want the filter set to high.
This allows you to cut the water off instantly when you remove the redstone signal. You no longer have to wait for the water to drain out of the duct work. This will shorten the ticks needed for water supply mode.
The steam extraction ducts are set up as normal with the servos configured for blacklisting water, or whitelisting steam, and redstone set to ignored.
Next, you simply attach MFR rednet cable to all of the fluiducts connecting for the water supply.
When the ducts receive a redstone signal, they let water into the high oven, and when the signal is removed, they stop inputting water, and start the steam conversion. Once the steam is generated, the fluiducts set for whitelisting steam, automatically pull out the steam and send it to your power generator.
The high oven can hold 20,000mB of fluid per ingot space inside. For a 3 high oven, this is 20,000mB. For an 8 high oven this is 120,000mB. Even though this much fluid can be placed in the high oven, steam conversion stops working if it is more than 1/2 full. For a 3 high oven, this is 10,000mB. For an 8 high oven this is 60,000mB. Since I am working with an 8 high oven, I need to keep the amount of water in it to 60,000mB or less.
Water will move through a fluiduct at a rate of 120mB/tick. Steam moves 3 times as fast with a rate of 360mB/tick. Here are some calculations with the number of ticks, the flow rate, and the total volume moved.
Water
Code:
Ticks Flow rate number of drains Total volume
10 * 120 * 50 = 60000
11 * 120 * 45 = 59400
12 * 120 * 41 = 59040
13 * 120 * 38 = 59280
14 * 120 * 35 = 58800
15 * 120 * 33 = 59400
16 * 120 * 31 = 59520
17 * 120 * 29 = 59160
18 * 120 * 27 = 58320
20 * 120 * 25 = 60000
Steam
Code:
Ticks - Flow Rate - Drains - Total volume
9 * 360 * 18 = 58320
10 * 360 * 17 = 61200
10 * 360 * 16 = 57600
11 * 360 * 16 = 63360
11 * 360 * 15 = 59400
12 * 360 * 14 = 60480
13 * 360 * 13 = 60840
13 * 360 * 12 = 56160
14 * 360 * 12 = 60480
15 * 360 * 11 = 59400
16 * 360 * 11 = 63360
16 * 360 * 10 = 57600
17 * 360 * 10 = 61200
18 * 360 * 9 = 58320
19 * 360 * 9 = 61560
20 * 360 * 8 = 57600
Using the numbers above, I maximized the amount of water vs the time vs the number of drains. With an 8 high oven, this turns out to be a time of 13 ticks, with 38 drains for water. This gives the absolute largest amount of water in the oven without going over the 60,000 mark. With the amount of space left over, 16 drains for steam output matched the best. This number is a little less important, but does affect the overall timer used with the oven. 16 drains for steam would reach the 11 tick mark.
To make use of this properly will require a MFR rednet controller. The first thing to set is the timer. I start the value out at 60, then go from there. Next, feed the timer output to a one-shot pulse, then to a pulse lengthener. This will decouple the on and off periods from each other allowing you to independently set the water input ticks. The pulse lengthener adds ticks to the 1 tick pulse, so make sure to subtract 1 from the numbers in the sections above. Next, AND the lengthened pulse output together with a lever so you can turn it on and off. The water will only flow into the high oven if both the clock timer is on AND the lever is in the on position.
Using these numbers, I was able to improve on my overall design and reduce the overall cycle from 112 ticks (timer set @ 56) to 80 ticks (timer set @ 40). This gives a 40% improvement over my previous numbers. I tried reducing the timer to 38, but after a minute or two of running one of the cycles couldn't complete in time and the oven filled up with water.
Previously, I generated 535mB of steam/tick. The new design generates 742mB of steam/tick. This works out to 1071RF/tick previously and 1482RF/tick now. (Actual RF increase of 38%)
Here is the front face of my test oven. The void drain is for when I got the timing wrong and filled up the oven with water, I had a way of draining the high oven without breaking the oven and having to re-heat it again.
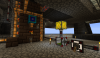