As someone who always preferred Tech mods, the addition of RotaryCraft to Monster has been a great new toy. After searching around, there isn't much info out there on it. I wanted to use hydrokinetic generators and found out they needed lubricant. I initially had a manual farm to get started. Once I had a few stacks of canola seeds, I made the grinder. Wow was it slow. You also need ALOT of seeds. After seeing Reika's video of his base, I found almost everything I needed to setup automated farms with RotaryCraft. This setup is a little on the large side. After how slow I started, I thought I would need this much to get the lubricant I needed. One nice thing about it being so large is that it only needs to run from time time, instead of always being on and drawing power. The fans and the fertilizer only use about 48 RF/t and make about 2k-3k canola seeds an hour. The grinder setup takes around 1500 RF/t, but can run through 5k canola seeds in minutes. Here's how you do it. Hopefully this helps with some of the stuff I couldn't find anywhere and figured out from trial and error.
The 16 fans are powered by a single magneostatic engine and power buses. It is set for 512 Nm and 512 rad/s for a total of 262.144 KW. You can see the range of the fan using the Angular Transducer. Click the fan and it will highlight how far the fan reaches. The power bus controller needs lubricant to function. The fans harvest and replant. All the extra seeds are blown into the water where the run into an ME Transition Plane to enter the ME network.
Here's the fertilizer setup. Water and bonemeal or apatite get fed into the sides and power into the bottom. The range of the fertilizer is based on torque, not speed, so when adjusting it to cover the area you want adjust the torque. To see how far it reaches, you have to just look at your crops for a few minutes and you will see a particle effect where it is working. It took a little trial and error to get the size right. Mine is running at 4096 NM and 4 rad/s for a total of 16.384 KW. It is at the same level as the dirt and under half slabs. Covering it doesn't appear to affect it, but I am not sure how many blocks high it reaches.
Next is the grinder setup. My 1st setup was so slow, so I played around and ended up with this. I have never seen anything go so fast in MC. A magneostatic engine at 1024 Nm and 8192 rad/s(max power) for 8.389 MW. It draws around 1500 RF/t, but it is so fast, you run out of materials to grind in 2-4 minutes so the energy cell barely drains. I have my energy cell outputting 2000 RF/t just to be safe. Power is fed into a 4:1 diamond gearbox set to speed. The power is split evenly with a shaft junction, steel shaft, and bevel gear. Me precision export buses feed it and itemducts extract items back into the ME interface. Lubricant is piped out of the bottom of them with fluid ducts. I originally set it up for lubricant, but now use it to grind certain ores as well as bones and apatite.
And then in a day or 2 of letting run while I was playing and I got this. Lol. It turned out to be a little overkill. A setup this size should easily keep a pretty huge base lubricated by only running for an hour or 2 every few days.
Here's one tip on using power buses. The controller needs lubricant to work. The power buses transfer power to themselves automatically. To transfer power to a machine from them requires a shaft or gear set to be put into the proper slot. Here is an example. Figured I'd share since these 2 things gave me the most headache when setting this up. It also would not work for some reason when i 1st set it up. I had to break all the power buses and replace them starting the power bus controller. Seems you may need to place the controller 1st.
The buses connected to the fans are like this. The fans are on their red face.
This is how the buses with no fans looks.
The 16 fans are powered by a single magneostatic engine and power buses. It is set for 512 Nm and 512 rad/s for a total of 262.144 KW. You can see the range of the fan using the Angular Transducer. Click the fan and it will highlight how far the fan reaches. The power bus controller needs lubricant to function. The fans harvest and replant. All the extra seeds are blown into the water where the run into an ME Transition Plane to enter the ME network.
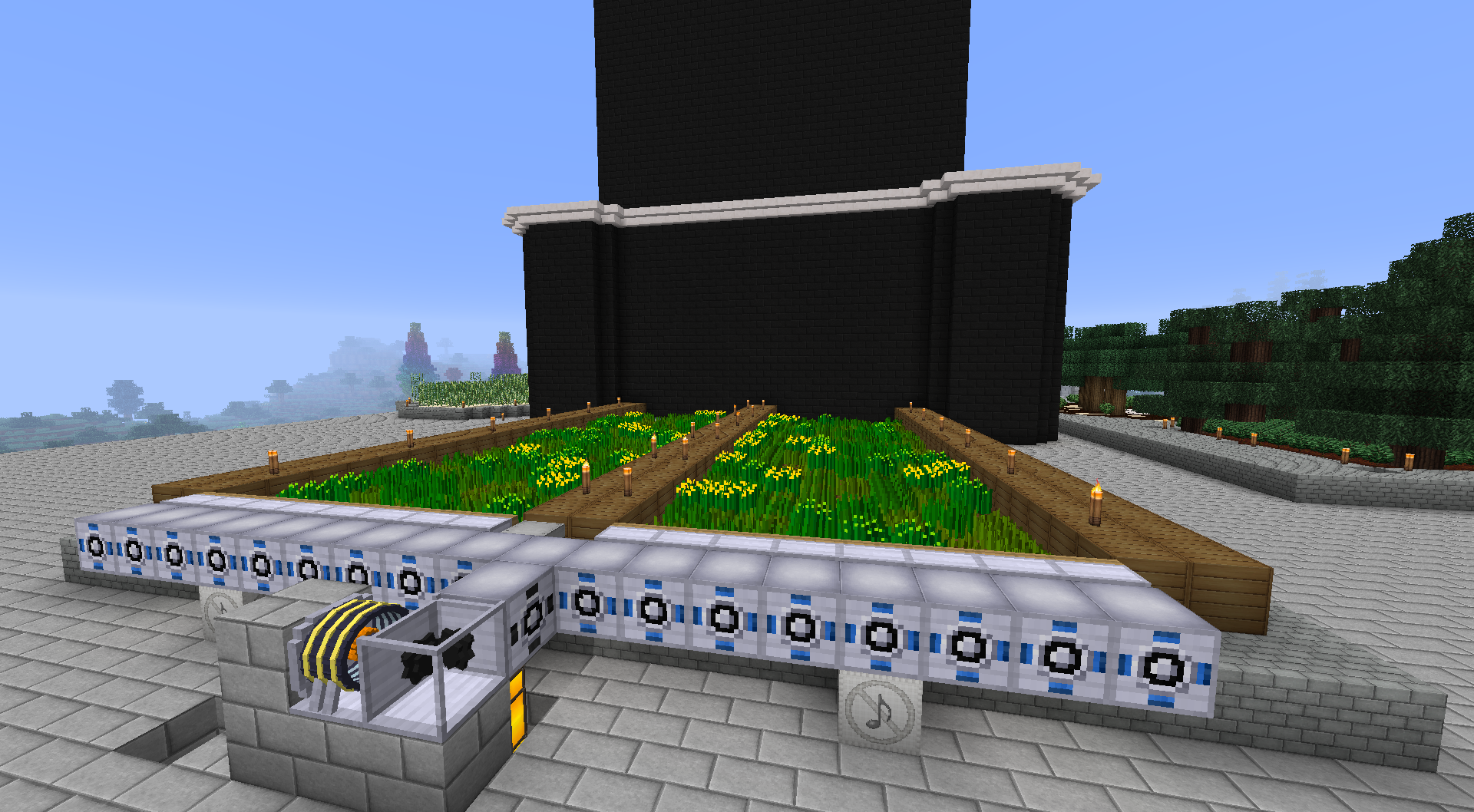
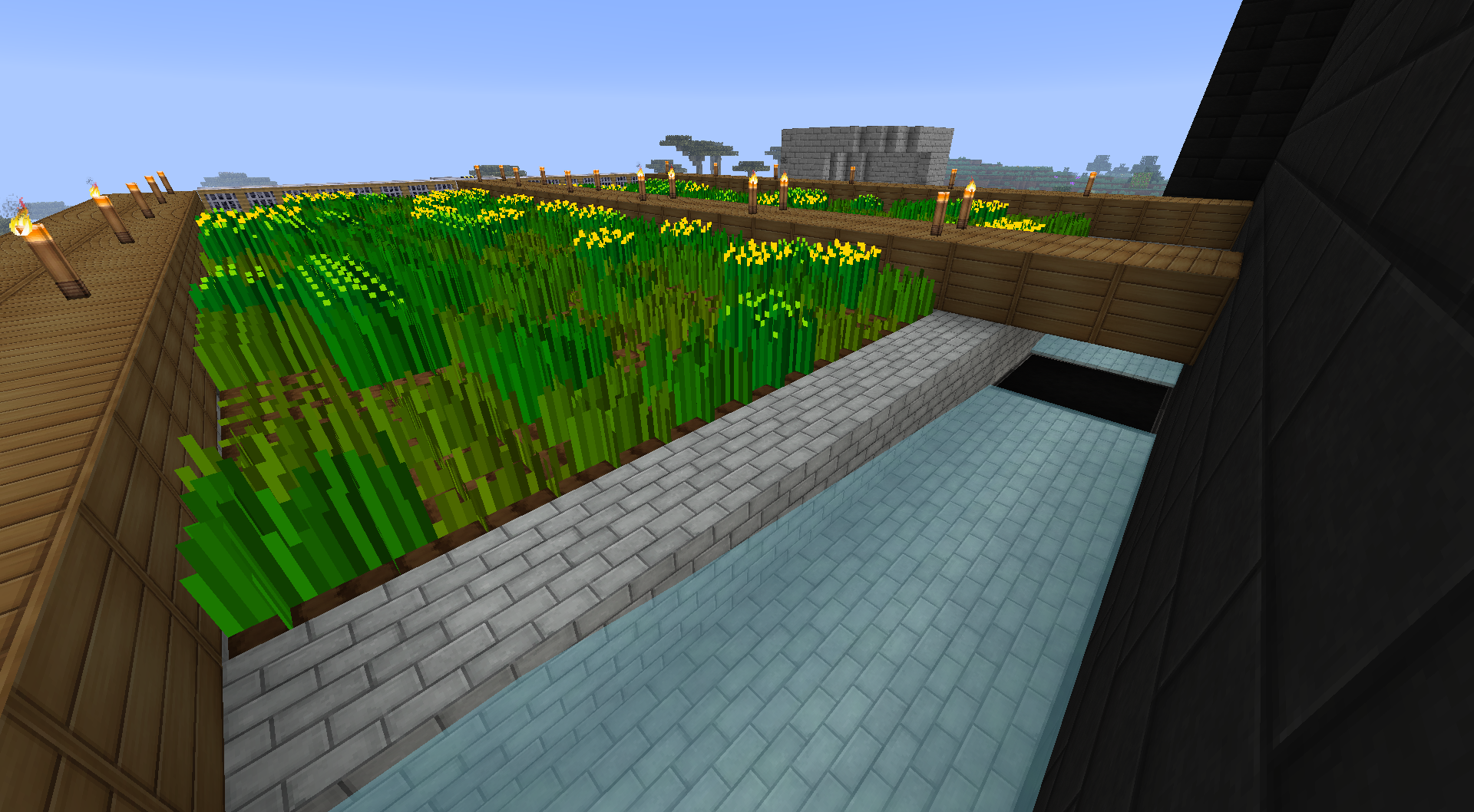
Here's the fertilizer setup. Water and bonemeal or apatite get fed into the sides and power into the bottom. The range of the fertilizer is based on torque, not speed, so when adjusting it to cover the area you want adjust the torque. To see how far it reaches, you have to just look at your crops for a few minutes and you will see a particle effect where it is working. It took a little trial and error to get the size right. Mine is running at 4096 NM and 4 rad/s for a total of 16.384 KW. It is at the same level as the dirt and under half slabs. Covering it doesn't appear to affect it, but I am not sure how many blocks high it reaches.
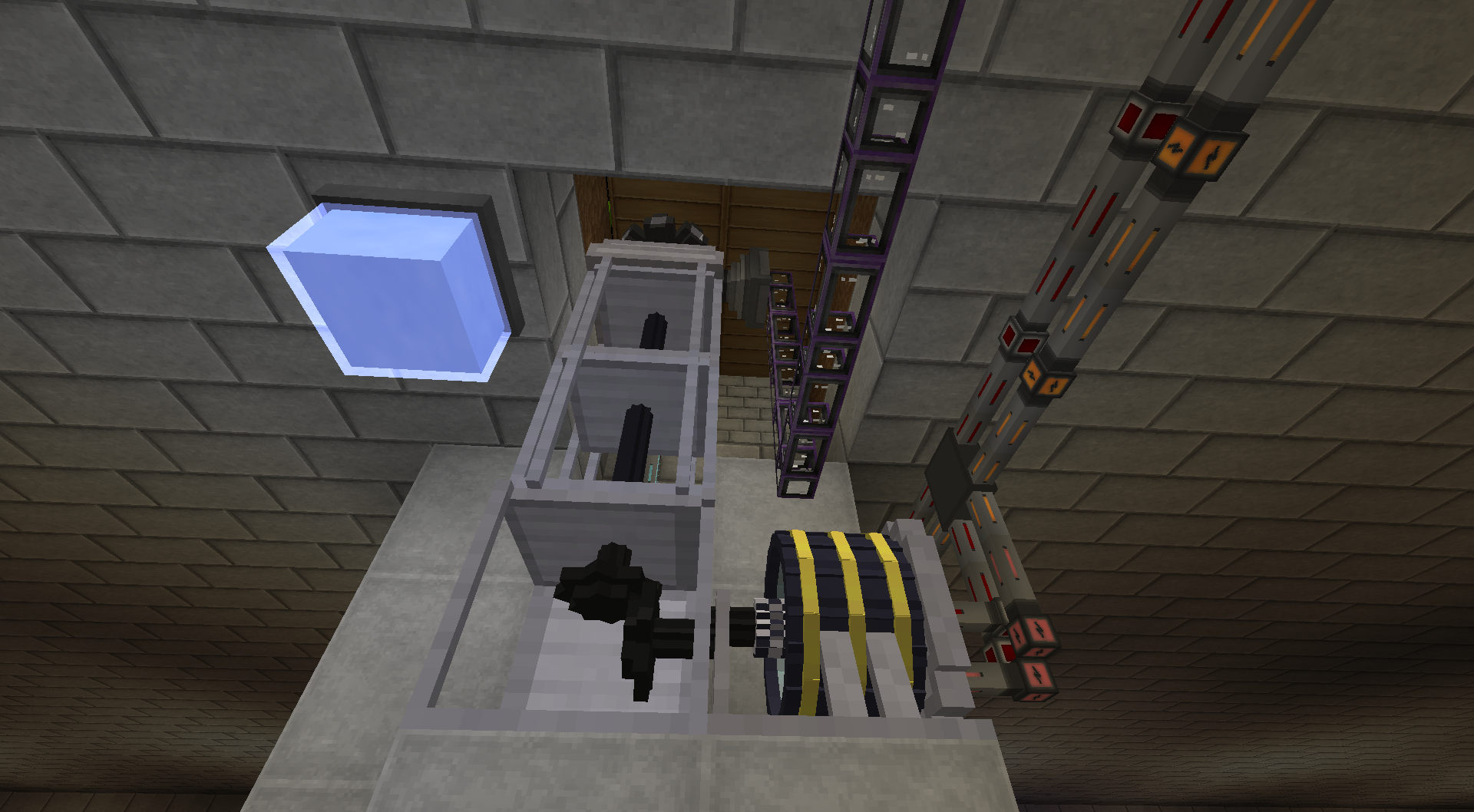
Next is the grinder setup. My 1st setup was so slow, so I played around and ended up with this. I have never seen anything go so fast in MC. A magneostatic engine at 1024 Nm and 8192 rad/s(max power) for 8.389 MW. It draws around 1500 RF/t, but it is so fast, you run out of materials to grind in 2-4 minutes so the energy cell barely drains. I have my energy cell outputting 2000 RF/t just to be safe. Power is fed into a 4:1 diamond gearbox set to speed. The power is split evenly with a shaft junction, steel shaft, and bevel gear. Me precision export buses feed it and itemducts extract items back into the ME interface. Lubricant is piped out of the bottom of them with fluid ducts. I originally set it up for lubricant, but now use it to grind certain ores as well as bones and apatite.
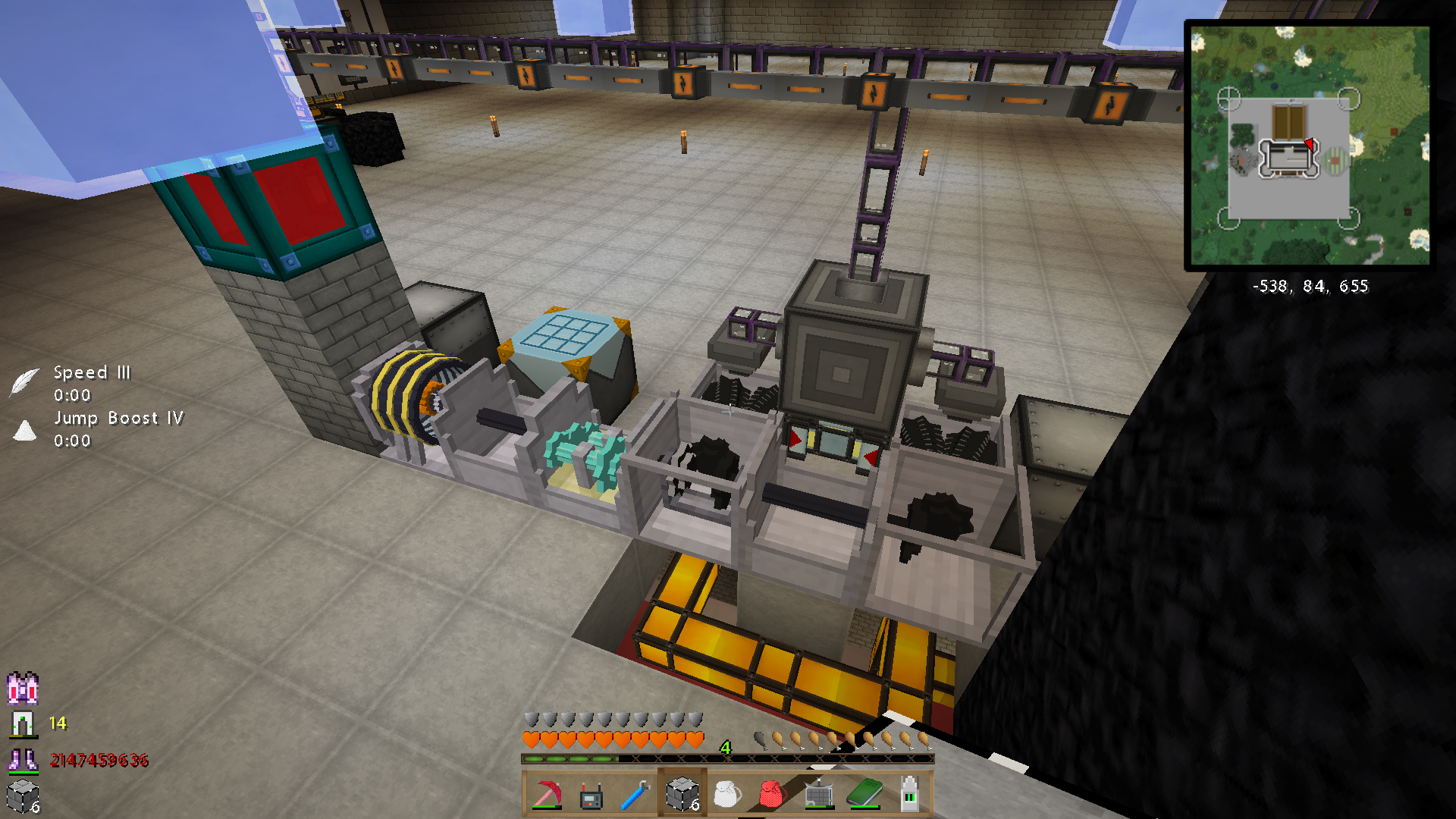
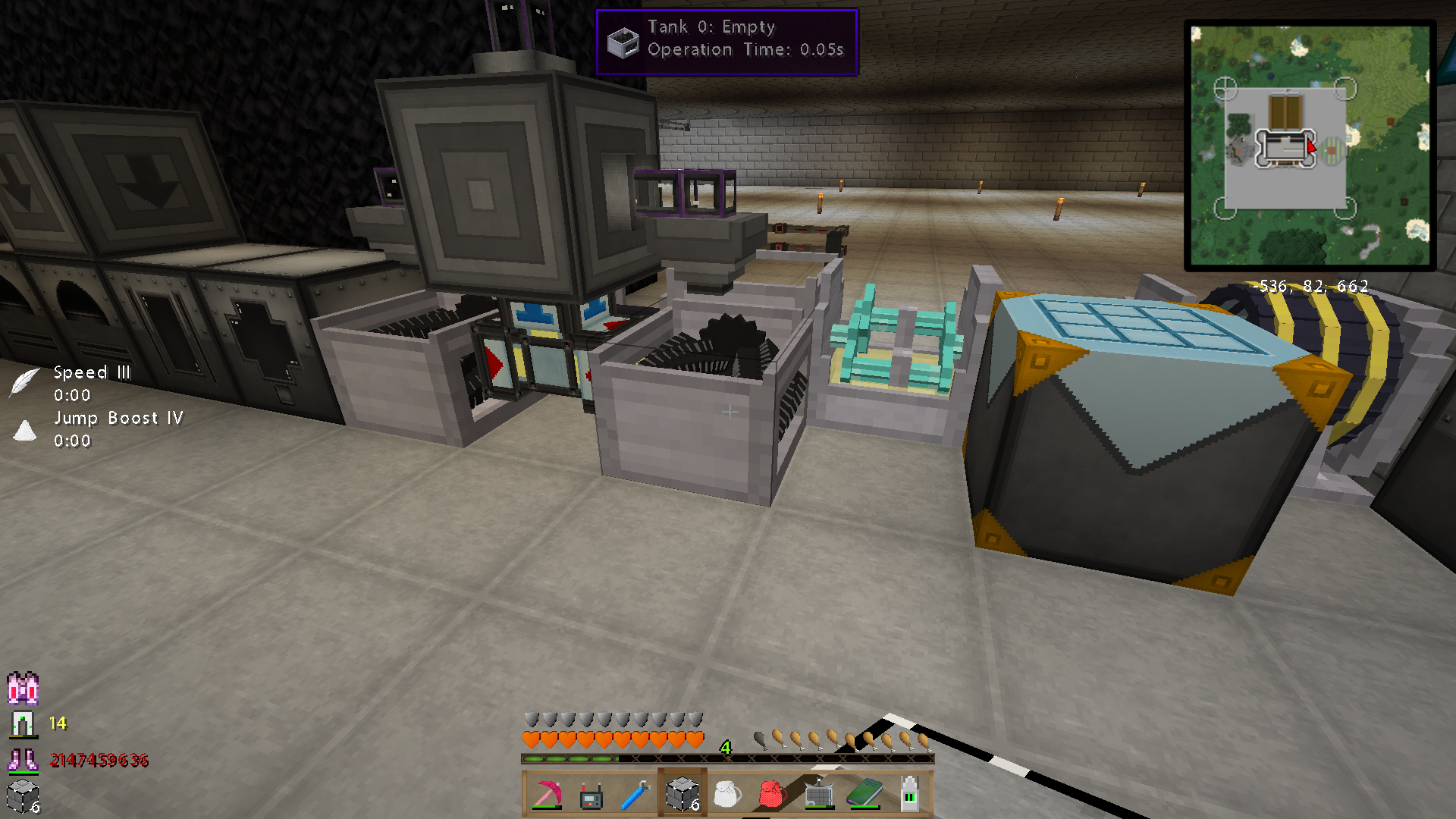

And then in a day or 2 of letting run while I was playing and I got this. Lol. It turned out to be a little overkill. A setup this size should easily keep a pretty huge base lubricated by only running for an hour or 2 every few days.
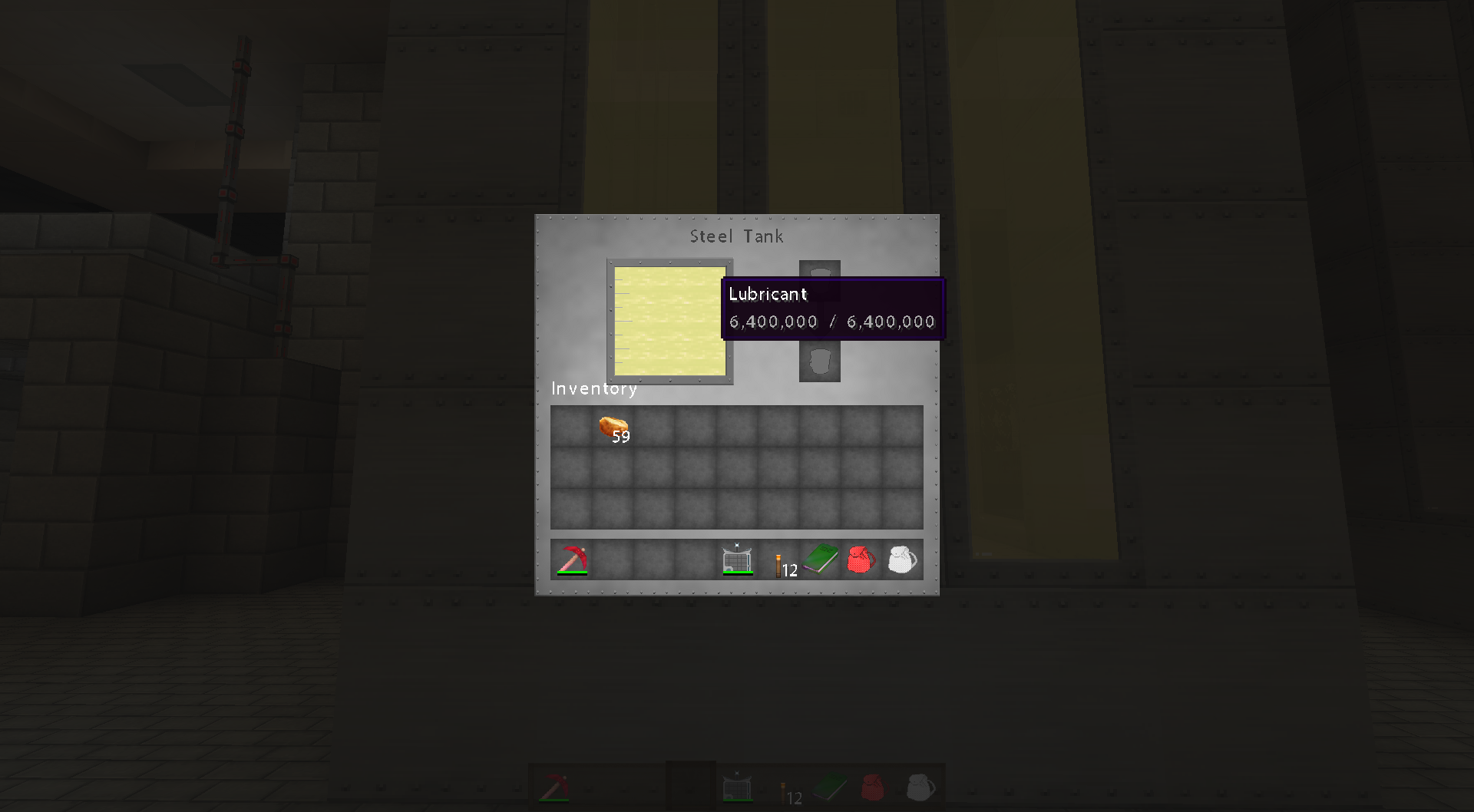
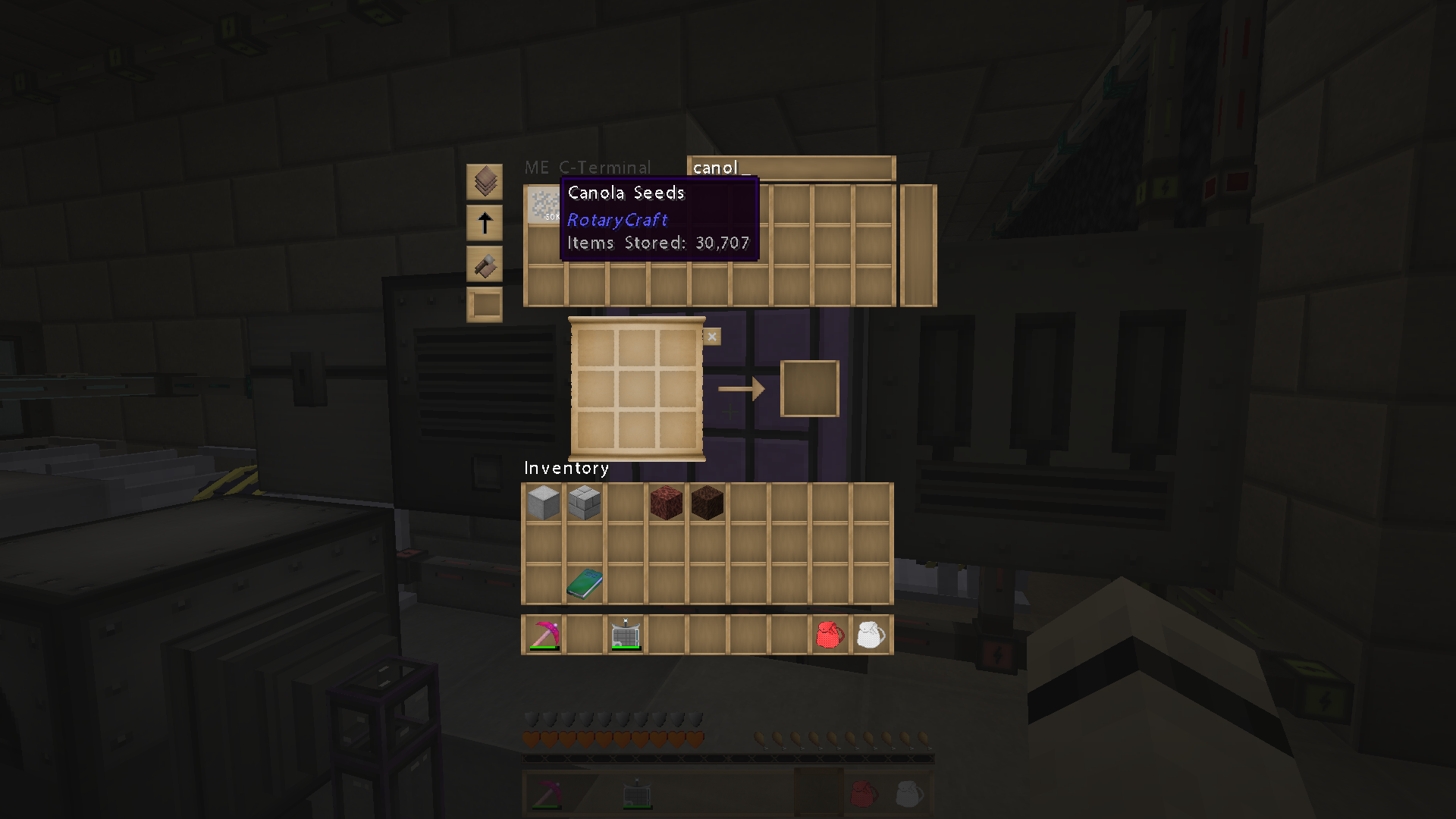
Here's one tip on using power buses. The controller needs lubricant to work. The power buses transfer power to themselves automatically. To transfer power to a machine from them requires a shaft or gear set to be put into the proper slot. Here is an example. Figured I'd share since these 2 things gave me the most headache when setting this up. It also would not work for some reason when i 1st set it up. I had to break all the power buses and replace them starting the power bus controller. Seems you may need to place the controller 1st.
The buses connected to the fans are like this. The fans are on their red face.
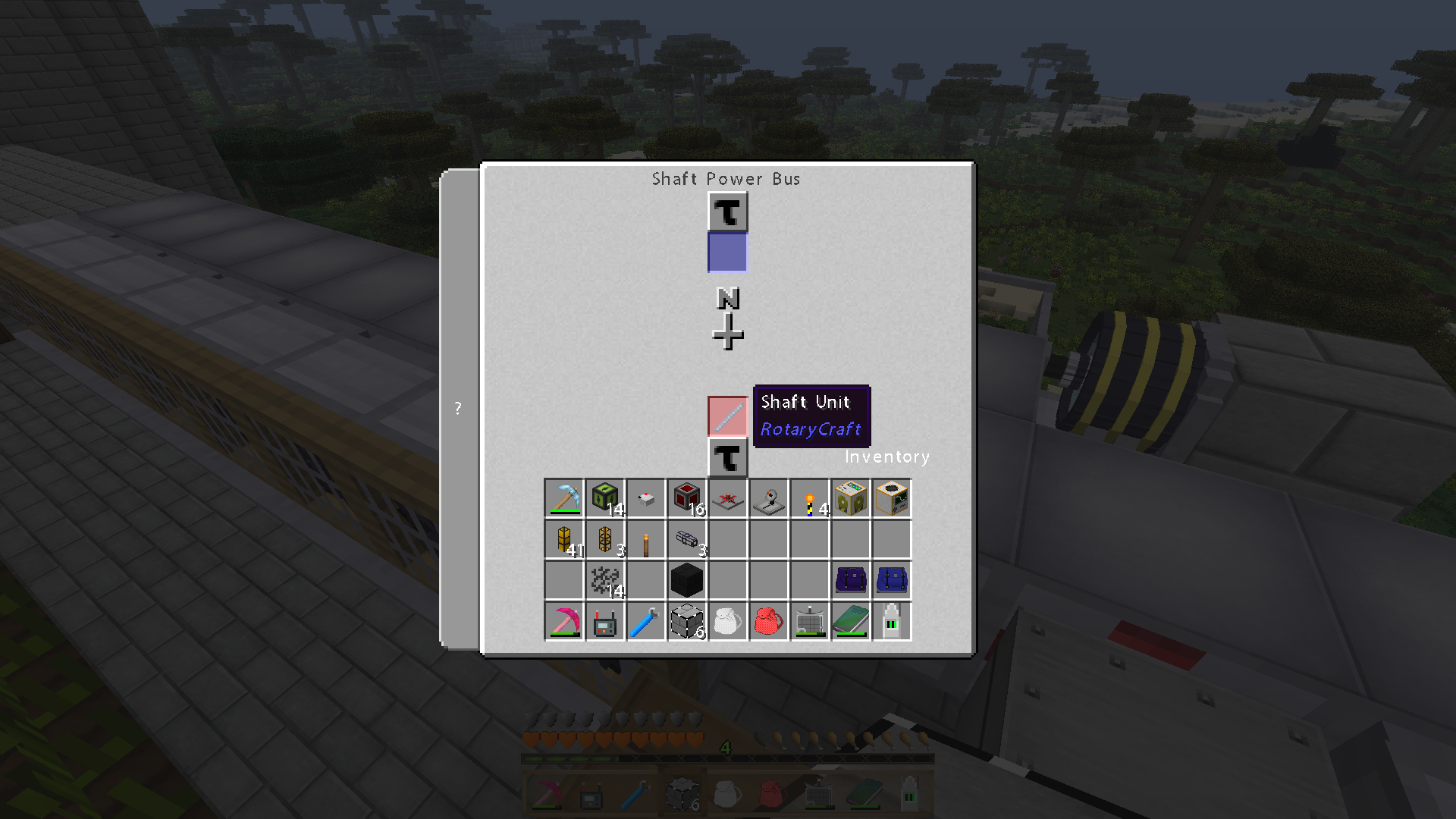
This is how the buses with no fans looks.
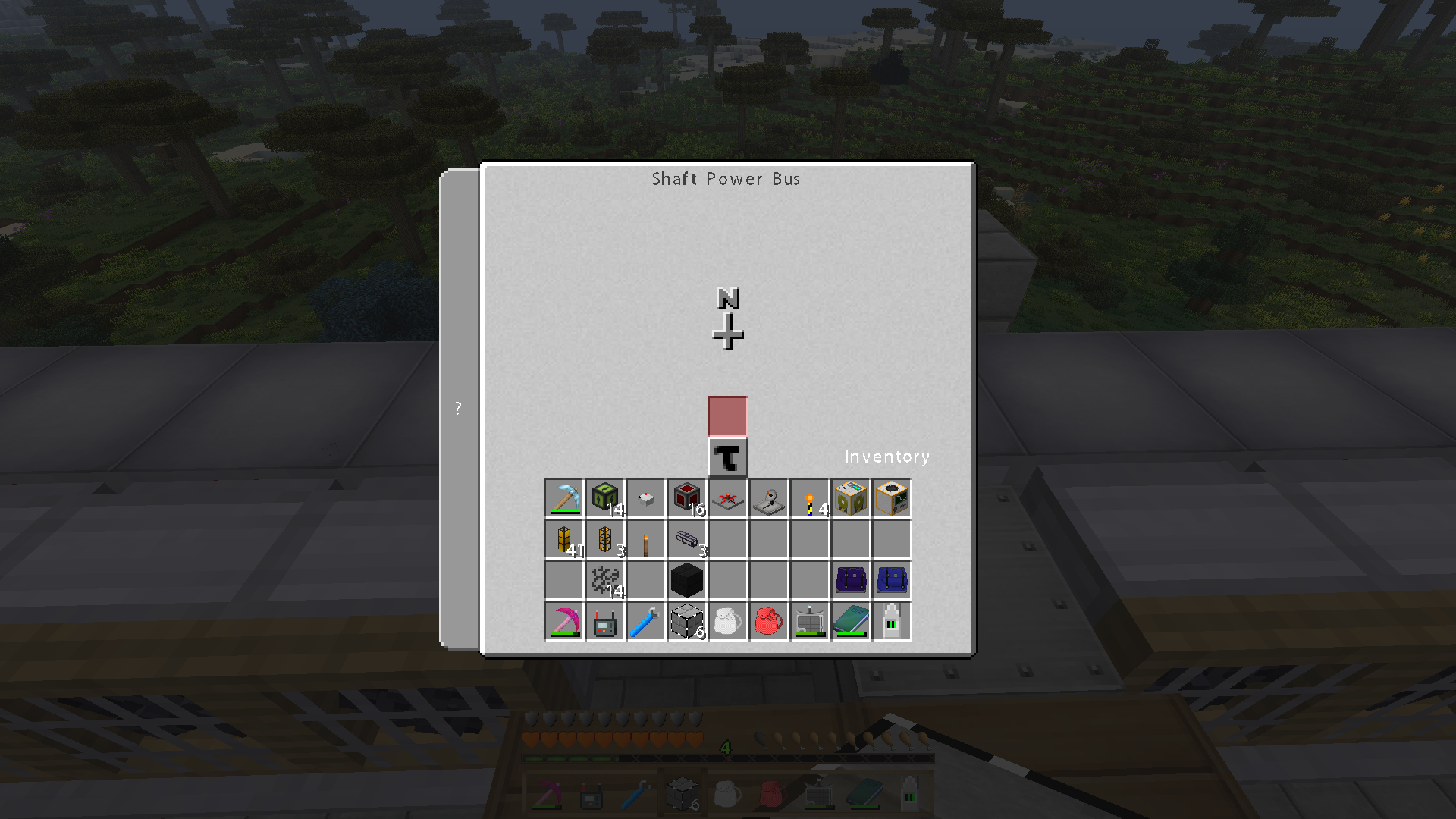